藤山哲人の実践! 家電ラボ
国内生産へのこだわり! 日立の家電生産ラインはInspire the Nextだった!
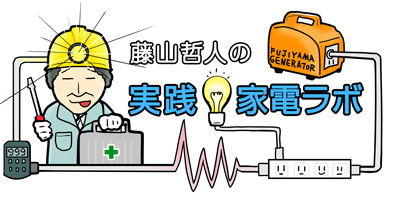
国内生産へのこだわり! 日立の家電生産ラインはInspire the Nextだった!
2019年11月13日 00:00
日立の工場は、常陸にあるってのは都市伝説じゃなかった! 東京から上野東京ラインに乗って2時間半、特急なら1時間半で行ける常陸多賀という駅がある。
駅前にはコンビニがなく、飲み屋と薬屋が数店舗あるだけの地方駅。しかし駅の反対側に回ると、日立の巨大工場がある。歩けど、歩けど工場の敷地が続き、20分歩いてようやく四角の敷地の1辺。とにかく広い。
敷地を貫く日立専用の鉄道引込み線も豪快! 今は廃線になってしまったが、海沿いの国道に沿って日立専用の引込み線があり、常陸多賀駅の両隣の駅までつながっている。その昔は、部品や製品、薬品などを積み込んだ貨物列車が走っていたのだろう。
まったく関係ないが(笑)、地図で□で囲った「湯楽の里」は太平洋が一望できる露店風呂がある日帰り温泉施設。全国露店風呂を旅する筆者の中で、ナンバーワンの眺望なのでオススメ!
話は戻って、上半分の砲弾型の敷地には3~4階建てのビルの大きさほどある、工場や発電所用の変圧器などを作る工場がある。そしてコレを運び出す常磐線側の引込み線はいまだに現役。
だから常陸多賀駅は、貨物マニアには超有名な駅だ。変圧器を積載する専用の超大型(重量)運搬貨物車(シキ)は、車輪が1両に12軸ある超特殊車両なのだ。
今回は敷地の南半分を占めている家電関係の工場にお邪魔した。お察しの通り駅に隣接している工場なのに、正門まで車で10分かかる……。とにかく広い……。
多賀工場は日立の主力家電製造の心臓部。セキュリティも堅牢!
ここは、洗濯機や掃除機、炊飯器に電子レンジ、IHクッキングヒーターにシーリングライトと、日立の主力家電商品を製造している心臓部だ。なのでセキュリティは厳しい。
工場建屋の内部の撮影は可能だが、外観は一切撮影不可。一部の建物の撮影はOKだが、「この向きのみ」という画角制限も付く。もちろん工場内の道路も撮影不可だ。
今までたくさんの工場見学をさせてもらった筆者だが、この厳しさは柏崎刈羽の原子力発電所クラスだ。敷地内のどこで何を生産しているのか、内部の通路はどうなっているのかは一切秘密なのだ。とはいえ今はGoogleMapのタイムラインを使えば、ドコを歩いたか分かるじゃん! と調べてみると……。
なにっ! 移動履歴がまったく残ってない! マジか! 敷地内はGPSジャマーの電波が張り巡らされているのか?
こんなに厳重なセキュリティで、これまで秘密のベールに包まれていた日立製作所 多賀工場。どこまで解説しても怒られないか!? ギリギリのラインを探っていこう。業界の方は注目だ!
作業台(カラクリ)までハイテクな日立の製造ライン
まずはキャニスター式掃除機の製造ライン。作っているのはコレ。
この掃除機の特徴は「掃除機といえば紙パック」という根強い人気に応えた「軽さ」と「吸い込むパワー」。吸引力の指標となる吸い込み仕事率は340Wで、一般的なサイクロン掃除機の倍ほど。
じゅうたんの奥に潜む砂ゴミもパワーで吸い込むという、体育会系掃除機だ。その秘密は、吸い込み口から紙パック、そして吸引モーターまでの風の流れが一直線で、抵抗になるものが一切ない点。
市販の紙パックは水漏れするが、日立純正の紙パックだと水の分子を通さず空気のみを通す極小の穴となっている。この紙パックとフィルターと併せて微細な粒子のゴミでも99.999%捕獲できる点が特徴だ。
またストレートで強力ゆえに、紙パックのモーターに近い後部にゴミがたまり、微粒子などによりパックの目が詰まってしまう心配もある。一般的な掃除機なら、それがパックの交換時期になるが、日立は紙パック前面からも吸引する空気のバイパスを設けているので、パックがゴミでパンパンになるまで吸引力が落ちないところも特徴だ。
加えて本体のダイヤモンドカットのようなデザインは、本体の強度を保ちながら、裏面のリブ(格子状についている梁)を少なくし、樹脂を少なくして軽くしている。
カットもよく見ると三角が基本構成になっているので、鉄橋と同じようにトラス(三角を組み合わせた)構造で曲げや引っ張り、圧縮やねじり荷重を分散させ、肉厚を薄くしても強度を保たせているようだ。
さてそんな掃除機を作っている現場がコレ。
「えっ! こんなに小っさいの!?」と思うかも知れないが、これが生産ラインの全景! 画面左にあと100人いるわけでもなく、向かい側に何百人いるわけでもない。
コレだけコンパクトなのは「セル生産」という方式を採用しているから。今でも体育館を何個もつなぎ合わせた建物の中に、長いベルトコンベアを設けて、「1人1工程」を担当する「ライン生産」も多くある。
これだと「モーターを設置する“だけ”の人」「そのネジを締める“だけ”の人」と、何百工程、何百人の人が必要。しかも作業をしている人は、かなり面白くない(笑)。半面、大量生産するのにいちばん効率的。ロボットで作業を自動化している場合も大抵ライン生産だ。
逆に「セル生産」では、最初から最後までの組み立てを一人でする。だから作業に変化があって面白いし、よし! 今日はみんなより30秒速く作ってみよう! とモチベーションの維持にもつながる。ただ問題は、掃除機1台分の組み立て方をすべて頭に入れていないとならない点。それゆえ生産ラインに出て一人前になるまでに、およそ1カ月の研修期間を要するという。
さてセキュリティーの厳しい日立の工場は、業界関係者も興味深々と思うので、作業台にググッ! と寄ってみよう。
まず目に付くのは、既製品の作業台ではなく規格品のアルミパイプ(質感から見てアルマイト加工)を組み合わせた「超」オーダーメードの作業台だ。通常アルミの丸パイプ(軽い製品だと塩ビパイプ)が使われるところだが、クランプを噛ませる溝があるパイプをメインに使っている。強度を持たせたり、何かをスライドさせるところでは、抵抗の少ないリブを持った専用のパイプを使用。
ジョイントもすごく豊富で、固定用のネジで傷ついたり、作業者の服を引っ掛けないよう、すべて座繰り(ネジの頭が飛び出ない)して、凹凸をなくしていた。
細かい部品は左右に設けた部品箱に入っていて、取り出しやすいように20~30度ほどの角度が付いている。さらに右側には、一時的に部品を置けるような引き出し式のミニテーブルも備える。部品の多い製品を作る場合は、このテーブルにも部品箱を置くと思われる。
またパイプの切れ端を使って、ペンや工具立てにしているのも面白い!
この風景は、工場見学を見慣れている人や、業界関係者は違和感を覚えるかもしれない。そう、妙に背中側がスッキリしているのだ。通常は部品を供給するカラクリ(一般的に坂道+コロになっていて、次々部品が繰り出されるところから「カラクリ」と呼ばれる部品ラック)が背中側に並び、作業者の手元があまり見えない。しかし日立の工場は、部品を前からコンベアで供給するようになっているので、背中側に部品ストックのカラクリがない。
作業台前の部品ストックは、何列かのベルトコンベアになっていて大きな部品、たとえば本体ケース、モーター、コードリール(巻き取り式コード)などが、作業者が前に手を伸ばすだけで取れるようになっている。
一般的な工場だと、振り向いて取るため作業効率が悪いが、日立では作業台から目を離さず部品が取れるのだ。部品を1つ取り出すと、コンベアで奥から部品が迫り出してくるのも面白い。よく見ると赤外線を使って、常に部品が作業者の前にあるかを自動で検出しているようだ。
日立のセル生産のスゴ技はコレだけで終わらない。通常完成品を流す作業者の奥は、部品供給をする自動運搬車の通路になっている。作業者の前に部品がないと赤外線センサーが検知し、自動運搬車がそのセルまで走って部品を供給してまわるのだ。
自動運搬車に部品を載せるのは人だが、当日の担当は1人だった。一般的な工場だと部品供給担当車が歩き回って、作業者の背中の部品ストックに補充して回るので、大幅な合理化が量られている(ライン生産の場合だと、作業者の背中まで自動運搬車が部品を運ぶところが多いが、セル生産の場合1人にたくさんの部品を供給するため、人力が多いようだ)。
さらに自動運搬車には、何種類もの部品をいくつも載せられるので、部品がなくなったセルまで走っていって、足りなくなった部品をベルトコンベアで作業者の目の前まで送り込むようになっている。
驚くべきは組み立てにかかる作業時間。この掃除機の場合、平均4分で組み立てるというのだ。平均なので、3分台で作っちゃう人もいるわけで、下手すりゃライン生産より短時間で作れてしまうのには驚きだ。手が小さく、手先が器用なひとが多い日本人ならではの、迅速セル生産ラインといえるだろう。
組み立てやすさこそ信頼の証。中心に作業員ありきのセル生産
次に見たのはスティック型掃除機。実物はコレ。
日立の新型スティック掃除機は、「軽くてハイパワー」という相反する難しい課題に挑戦したモデル。
そのパワーの源となるのは、「モーター屋、日立」独自のブラシレスモーターだ。一般的なスティック掃除機用のモーターは、インペラという翼を回転させ、前方から空気を吸い込み後方に空気を逃す。
しかし高速回転するスティック掃除機では、空気に粘性があるのでインペラの空気がうまく流れず、一定量の空気がモーター内を常にぐるぐる回って滞留してしまう。
そこで日立はインペラの周りにディフューザー(空気の流れを均一に整え拡散する翼)と呼ばれる翼を2枚設けた。
インペラに近い内周のディフューザーは、インペラに絡みつく空気を大工さんのカンナのように削り取るもの。第2のディフューザーは、横方向に剥がした空気を、後方に曲げるものだ。
こうしてモーター内に滞留する空気をなくし、空気の流れをスムースに方向転換することで、同じモーター、同じインペラを使っていても、よりたくさんの空気をパワフルに吸い込めるようになっている。
日立では縦2列に配置されたディフューザーなので、「タンデムディフューザー」(バイクの前席と後席、戦闘機の前席と後席があるタイプは「タンデム」シートと呼ばれるアレと同じ)とカッコよく呼んでいる。名前負けしない、流体力学を活かしたすばらしい応用だ。
さらに以前と同じサイズの筐体に、ゴミ捨てレバーなる機構も設けている。スイッチ下の水色のレバーを引くとダストカップのふたが開き、ゴミをワンタッチで捨てられるという機構だ。タダでさえ部品が密集しているスティック掃除機だけに、機能ひとつ加えると構造が複雑になり、製造も難しくなるのは言うまでもない。
その生産ラインがこちらだ。
ライン全体の規模は先のキャニスター型と同じで驚くほど小さい。また背中側に部品のカラクリもない。が、先のキャニスターとまったく異なるのは、作業台の机だ。
キャニスターのラインは、平らな机になっていたが、スティック掃除機の作業台は、家電のパッケージを開けると入っている発泡スチロールのように起伏があり、そこに部品がキッチリ収まっている。
そう! このラインは先のキャニスターをさらに進化さえたトレイ方式のセル世産になっている。日立ではこれを「キットチャージ」「スマートセル方式」と呼んでいるようだ。
トレイ方式は、まず必要な部品集めから始まるので、作業台の前に部品のピックアップから見てみよう。
ここでは手前と奥で、作業台で見たのと同じ凸凹になったトレイに必要な部品をピックアップしてはめ込んでいる。一般的なピックアップ方式だと、トレイやコンテナを持って部品棚に行き、部品棚のランプが付いている部品をピックアップしてコンテナに入れていく。同じ部品が複数必要だと、ランプの代わりに数字が表示される場合も。
もう少し進化すると、トレイが間仕切りされていて、必要なパーツを同じ番号の間仕切りに中に入れていくなんてところもある。
しかし日立のトレイ方式は、部品の形に穴の開いた作業順に部品を並べられる立体トレイに、部品をセットすることから始まる。すべての凸凹に部品がセットされていればセット完了、抜けがあればピックアップ漏れがすぐに分かると言うものだ。
作業者にしてみれば、必ずトレイの同じ位置に、同じ向きで、しかも取り出しやすい方向に部品がセットされているので、組み立てでは目を離すことなく作業できて効率がいい。たとえるなら、医者が外科手術をやるときに、隣に優秀な器械出し看護師がいるようなものだ。汗は拭いてくれないが……。
さてトレイにすべての部品をセットすると、カラクリで隣に並ぶ作業台に送られる。
一方作業台の方は……。組み立てを終えると、空のトレイが傾き、奥のカラクリに繰り出される。お察しの通り空のトレイは、コンベアに乗って部品のピックアップ工程に回る。そして作業台には、部品がセットされたトレイが流れてくる! これは凄い! 初めて見た!
作業台の前にあるピンクの階段状のボックスは、ネジの送り出し機。これはネジの頭を上にして、1本1本送り出すという機械だ。作業者はパチンコのチューリップのような開きにドライバを差し込むだけで、手を使わずにドライバにネジをセットできるというわけ。
2台あるということは、太さ(または長さ)の違うネジ2種類だけでスティック掃除機ができているとうこと。部品をそこまで集約する設計技術も凄い!
また小さな部品は、作業者の前にあるボックスに入っているので、ここから取り出して組み立てるようになっている。はめ込み式の部品も非常に多く、あれよあれよという間の3分で1台完成。脅威のスピード。コレ、俺が分解したら30分かかりますわ……。
できあがった完成品は、足元を通っているコンベアに流して終了。
実は、先のキャニスター式も完成品の流し方は同様になっているのだが、ちょっと伏せておいた。なぜなら、1台完成すると黒い平らな作業台が圧縮空気で奥に移動、まるで電車のドアが開くような感じで引っ込むのだ。
そして見えるのが足元のコンベア。大きなキャニスター掃除機でも、作業台の天板が開くのでラクにコンベアに乗せられるというわけ。
多種多様な生産ラインを数十も見学してきたけれど、こんなカラクリは初めて見た! 技術の日立は、生産ラインのカラクリまで、Inspire the Next! 次世代のひらめきっす! 俺もInspiring!
さて完成品は、ドコに行くかというと「検査工程」。この検査工程は、一切の撮影が禁止なので、写真の構図がみんな同じ(笑)。とはいえちょっとだけ説明しておくと、全量検査を実施していて、数台ある検査器に完成品をセットすると、色々な動作テストと測定データから、コンピュータが自動的に性能を判断しているようだった。
見学中には見られなかったが、おそらくロットアウトがあると、エラーを知らせるようになっているのだろう。検査を終了すると、人が検査器から外し、別フロアにあるパッキング工程に回るようになっている。
画像認識で作業工程をチェックするInspireなセル生産
次に見たのは、ロボット掃除機のミニマル! 一般的なロボット掃除機より小さいので、イスの足の間まで入り込んで狭い隙間もきれいにしてくれるのが特徴。また最近ファームウェア(中のプログラム)がアップデートされ、壁への衝突回数が大幅に減ったなどの進化をしている。
こちらの生産ラインも規模は同じだけど、トレイ方式からさらに進化した作業工程監視システムが組み込まれている作業台。
ロボット掃除機だけに部品の数も格段に増え、それだけ組み立て手順も複雑かつ長くなるので、本来ならセル生産に向かない製品。しかし、これまでのセル生産の生産技術に加えて、コンピュータアシスト&画像認識システムを加えたのが、日立の凄いところだ。各メーカーともに、しのぎを削って開発している次世代セル生産システムでもある。
基本はスティック掃除機のトレイ式セル生産と同じ。しかし作業が複雑なので、トレイの上では組み立てず、カメラが見通せる平たい作業台の上で行なうのが特徴。
上流の部品のピックアップ工程は、ご覧の通り。スティックの3倍ほどある部品の数々を、トレイの規定の位置に収めていく。トレイにはパーツ番号が振ってあるわけでもなさそうなので、実はいちばん熟練工じゃないとできない作業がこの作業なのかも? ちょっと注目して欲しいのは、部品をピックアップ中のトレイの角度。これを覚えて、次の工程を見て欲しい。
すべての部品をセットすると、カラクリを通して組み立て工程に流される。
組み立て工程に流れてきたトレイは、部品が取り出しやすいように60度ほど傾斜が付いている。これもカラクリが自動的に傾斜を着けてくれるのだ。
先に説明したネジ送り出し機は、ここも2台。なんとミニマルも2種類のネジだけでできているのだ! スゲー!
他の掃除機と違うのは、電線(コネクタ)の量。とにかく似たようなコネクタがたくさんあって、マイコンが乗っている基板と、本体各部のセンサーやモーターなどを接続していかなきゃならない。もちろん設計段階で、誤結線防止のために特定の電線は、特定のコネクタにしか刺さらないようになってはいるものの、組み立ては難しい。
そこで日立では、作業台の上にカメラを備えて、作業工程と作業完了時の状態を見比べ、画像認識で正しい作業が行われたかチェックされ、問題なければ次の作業手順書を作業台前のディスプレイに表示するようになっている。
このシステムにより、組み立てが複雑な製品でもセル生産でき、手順や作業の誤りもその場でチェック・修正できるため製品の歩留まりもよくなる。さらに作業員の習熟度の向上にも貢献するという。
通常なら熟練者が立ち会って、作業者の動きと製品を一部始終チェックする。しかしこのシステムを使うと、熟練者の立会時間を最低限にできるだけでなく、作業者の習熟の時間も早くなるというのだ。おそらく手順書を見ながら「習うより慣れろ」ということだろう。
さて、こうしてコンピュータアシストライズされた作業台では、7分に1台のミニマルができるというから驚きだ。
「日立」。日本でいちばんお客さんに近い家電メーカー
今まで機密という鋼鉄のベールに包まれて、目にすることができなかった日立の掃除機の製造ライン。新製品の発表会では、いつもエンジニアが緊張しながら、たどたどしいプレゼンをするのだが、こと機能やしくみの質問をすると饒舌に答えてくれる(笑)。
そんな根っからのエンジニアが多い日立だけに、その工場も驚くほどシステマチックになっていた。まさに日立が長年掲げているキャッチ「Inspire the Next」だ。
製品の新しい機能やより使いやすいメソッドが、エンジニアの「Inspire the Next」で次世代のひらめきを製品に吹き込んでいる。今回は生産ラインを中心に取り上げたので、記事から漏れてしまった、掃除機の静音性の技術などもひらめきのひとつだ。
地元常陸で限りなく合理的にものづくりをして、よりよい1台の製品を製造するという日立の姿勢が生産ラインから見て取れた。
現場の作業員のみなさんからは、日々「こうすればもっと効率がいい」「こうした方が間違いが少なくなる」などの意見が出るという。生産技術部という別のセクションが作ったお仕着せの生産ラインをしぶしぶ使うのではなく、ライン担当が製造ラインを日々改善して、より良い製品を作るようにしている点も、作業者中心の日立のあり方を代表している。
そこには他社とは一味違うエンジニアのInspireと「日本製」の信頼、お客さんと製造者の身近な距離感があった。それが日立が掲げるもうひとつのコピー「ハロー! ハピネス」と「360°ハピネス」だ。日本でいちばんお客さんに近い会社。それは日立なのかもしれない。